Der selbstgebaute Flugsimulator
Fliegen. Jederzeit. Überallhin. Und zum Abendessen wieder zu Hause sein. Für diese Vision gab es für Stephan Buchmann nur eine Lösung: ein Flugsimulator.
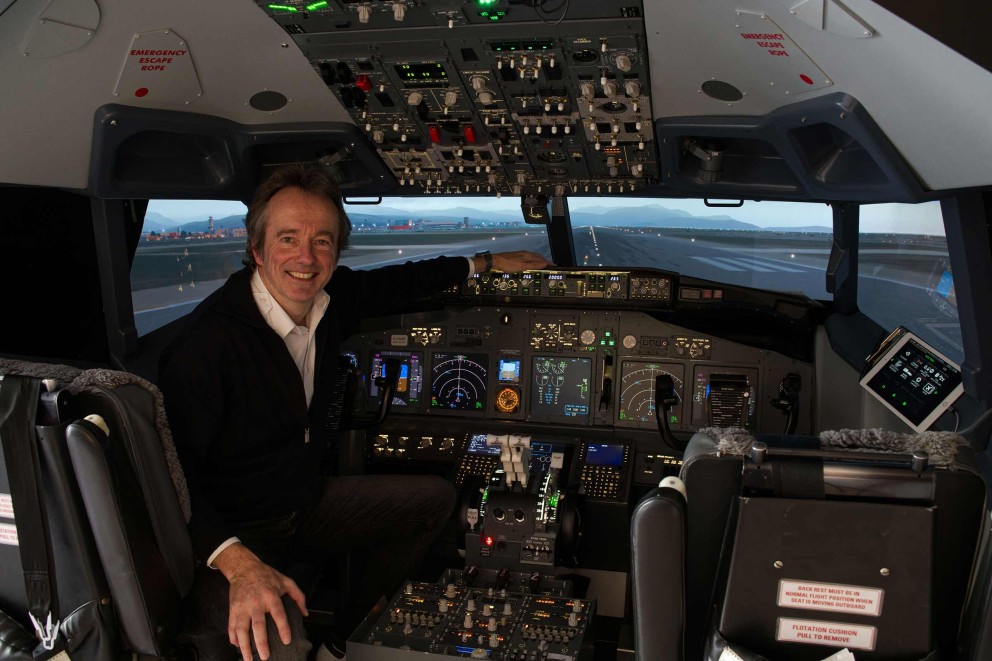
Fliegen, ohne wirklich abheben zu müssen. Das wollte Stephan Buchmann aus München, wann immer er wollte. Sein Traum: ein eigener Flugsimulator. Im Nachbau des Cockpits einer Boeing 737. Flugkenntnisse? Hatte der gelernte Tontechniker, inzwischen Angestellter in einem Technologieunternehmen, dank seines Pilotenscheins. Und handwerkliches Wissen? Beim Vater, Elektrotechniker, von klein auf abgeschaut. Den Rest: selbst beigebracht.
Die Herausforderung: die richtigen Maße und Komponenten finden. In Internet-Gruppen suchte er Baupläne und entschied: Er macht sein eigenes Ding. Nicht nach Vorlage. Plante über ein Jahr lang. Alles, was er nicht selber bauen konnte, bestellte er in aller Welt. Fünf Monate später kommen die Komponenten an. Die Qualität: nicht immer die beste. Dann alles von vorn: bestellen, hoffen, abwarten.
Stephan Buchmann
Ein weiteres Jahr später: Stephan hat alle Komponenten beisammen. Mietet eine Werkstatt an, legt Baumaterialien und Werkzeug bereit. Sein persönliches Ziel: Nach einem Jahr soll sein Flugsimulator fertig sein. Doch bald merkt er: Außenhülle, Schalter und Panels der 737 selber bauen, das kann Jahre dauern. So lange will er nicht warten.
Er legt los. Beginnt mit der „Base“, dem Boden, auf dem später das Cockpit stehen soll. Dann geht’s weiter mit dem Steuerrad, der „Yoke“, und zwei Subwoofern für den Sound, die in den Boden eingelassen werden. Hier ist Fingerspitzengefühl gefragt. Elektronik verlegen, überprüfen, ob alles läuft. Dann darüber Holzbodenplatten verlegen. Alles genau abmessen, zuschneiden, verschrauben. Um die zwei 737-Original-Pilotensitze zu montieren, muss er erst die Unterseiten der Sitze anpassen. Das Problem: Das Cockpit-Modell ist neuer als die Pilotensitze, die Mittelkonsole – hier sind Sprechfunk- und Navigationsfunkgeräte, Transponder, Feuerlöscher-Panels angebracht – breiter als bei der älteren Version. Die Sitze sollen also nicht nur gerade nach hinten geschoben werden. Stephan ersetzt die alten, geraden Schienen durch gebogene – in Form eines J, auf denen die Sitze zur Seite gleiten. Dann die Ruderpedale einbauen. Beide Pedale – Captain links, First Officer rechts – werden mit einer Stange verbunden. Maß nehmen, kürzen, Gewinde mit Gewindeschneider bearbeiten. Angeschlossen werden die Pedale an einer USB-Interface-Karte. So sind sie mit dem PC verbunden. Anfangs ist Stephan optimistisch: Geht sicher alles fix, bestimmt kann er schneller in den Flugsimulator steigen als gedacht. Falsch gedacht: Die teils kleinteilige Arbeit zieht sich. Freunde packen manchmal mit an, dann geht’s schneller. Dauert trotzdem. Rund vier Wochen allein für den Boden.
Stephans persönliches Highlight: der Bau der Projektionsleinwand, einer runden Holzwand, mit 220 Grad etwas größer als ein Halbkreis. Auf diese acht Meter lange Wand wird später die Außensicht der Flugsimulation projiziert.
Mit einer Computer-Software plant er vorab. Mit Papier, Bleistift und Geodreieck schreitet er zur Tat. Will aus Spanplatten ein rundes Gestell bauen, um darin die Projektionsleinwand anzubringen. Den Radius von 2,40 Metern zeichnet er mithilfe einer Schnur auf die Spanplatten. Für die vier Segmente braucht er jeweils vier Spanplatten-Bögen, insgesamt 16 Stück. Zwischen die vier Bögen kommen jeweils drei Balken, das Ganze vier Mal. Sohn Jan hilft mit. Schneidet mit der Kappsäge die 48 Balken aus 4 × 7 Zentimeter dicken Latten. Dann merken die beiden: Der Boden ist nicht waagerecht. Daher bei jedem Schritt: Wasserwaage raus, nachmessen, anbringen. Dann setzt Stephan gewölbte HDF-Platten ein und befestigt sie mit Schrauben. Vier Wochen später: Die Projektionsleinwand steht. Endlich. Jetzt der Feinschliff.
Ein Wochenende lang spachtelt und schleift Stephan die Projektionsleinwand ab. Darauf die Grundierung und eine spezielle Farbe, damit die Projektion später optimal sichtbar ist. Installiert die Projektoren. Zuerst die Projektoren an der Decke anbringen. Dann stellt Stephan fest: Die Decke vibriert, wenn sich der Nachbar von oben bewegt. Wie kann er das Problem lösen? Die Projektoren stattdessen auf einem Gestell montieren? Könnte funktionieren. Genau hier wird’s knifflig. Stephan muss sie an mehreren Wochenenden „warpen“ und überblenden. Wegen der gebogenen Leinwand müssen die Bilder der drei Projektoren mit einer Software entzerrt werden – das nennt man „Warping“ – und an den Übergängen überblendet werden. Mit Warping-Software entsteht in mehreren Anläufen – und mithilfe von Simulatorkollegen aus Spanien und der Schweiz, zugeschaltet per Chat – ein nahtloses 180-Grad-Bild. Ein Riesenfortschritt.
Stephan Buchmann
Jetzt fehlen noch Rückwände und Außenhülle. Hülle und Kunststoffteile für den Innenraum bestellt er in Kanada, baut die Elemente rund sechs Wochen lang zusammen. Geplant war nur ein Wochenende. Dann die Rückwände: echte Panels mit Sicherungen aus ausrangierten Boeing-737-Flugzeugen. Dank Rückwänden kann Stephan das Cockpit schließen, so fühlt sich der Flug noch echter an. Der Clou: Für Zuschauer lassen sich die Wände zur Seite schieben.
Dann das Aufwendigste: das Hauptpanel, eine Anordnung aus insgesamt acht Displays. Mit Reglern zum Kommunizieren und Navigieren. Sechs Displays baut Stephan selber ein. Schwieriger als gedacht. Trotz Erfahrung im Elektrobereich. Wichtig sind richtiger Winkel, richtiger Abstand zueinander und der Anschluss an die richtige Stromversorgung.
Damit „X-Plane“, die Flugsimulator-Software für die Cockpit-Technik, funktioniert, entwickelt Stephan mit einem Freund ein Plug-in, eine Software-Erweiterung. Gar nicht so einfach. Die Dokumentation der Hersteller ist oft unvollständig. Schalter für Schalter muss identifiziert und in die Software eingebunden werden. Also raus aus der Werkstatt, ran an den Computer.
Einige Wochen später dann der erste Testflug. Stephan setzt sich ans Steuer – und ist stolz wie Bolle. Nach kleineren Startschwierigkeiten läuft endlich alles – und Stephan fliegt von München aus quer um die Welt. Und das ohne Sicherheitskontrolle.
Stephans Flugsimulator in Zahlen
- Cockpit-Maße: 2,50 Meter × 2,50 Meter – Leinwand 4,80 Meter Durchmesser / Höhe 2,50 Meter
- Planung: zwei Jahre
- Bau: ein Jahr
Text: Esther Acason | Fotos: Stephan Buchmann